9. Machine settings
Use this window to set the machine and perform maintenance operations.
General Tab
Configure the settings for the machine selected in the top window.
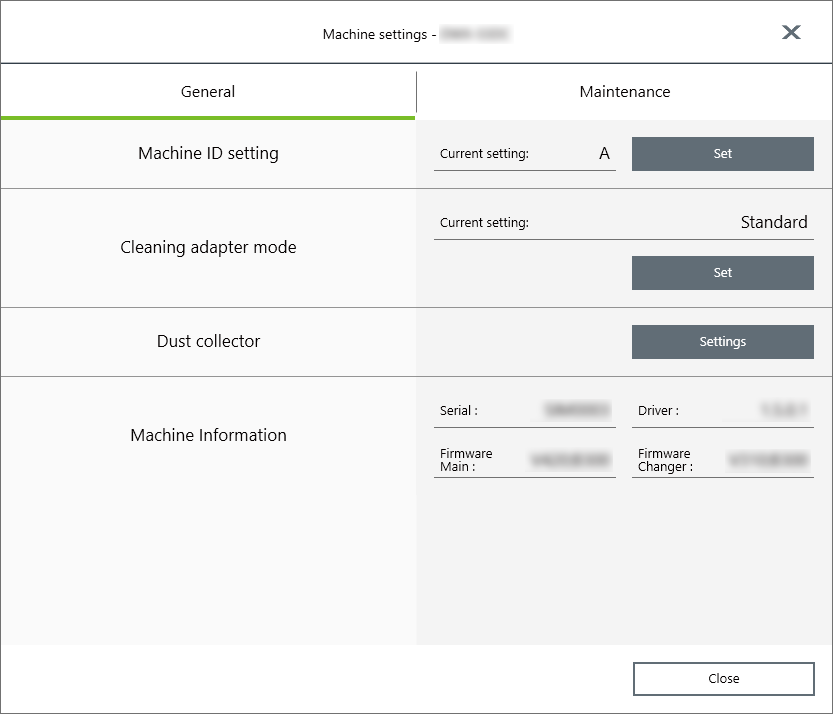
- Machine ID setting
- When multiple machines are connected to one computer, it's necessary to set IDs for the machines. Select the machine to use in the VPanel top window.
For detailed operation, refer to the Setup Guide of the model you are using.
DWX-53DC Setup Guide
- Cleaning adapter mode
- You can change the setting for blowing compressed air into the adapter to remove milling waste after milling finishes.
- Dust collector
- The suction power of the dust collector connected to the machine and the error detection settings can be changed.
If Error detection is set to On, an error message appears in VPanel when an error occurs on the dust collector.
For more information on other settings or detailed operation, refer to the documentation for the dust collector you are using.
- Machine Information
-
Serial: Serial number of the machine
Driver: DGSHAPE dental driver version
Firmware Main: Connected machine's main firmware version
Firmware Changer: Connected machine's disc changer firmware version
Maintenance Tab
On this tab, you can perform operations related to maintenance, including automatic correction of the machine and displaying system reports. When more than one machine is connected, the machine selected in the top window becomes the target for the operations. For detailed operations, refer to the User's Manual of the model you are using.
DWX-53DC User's Manual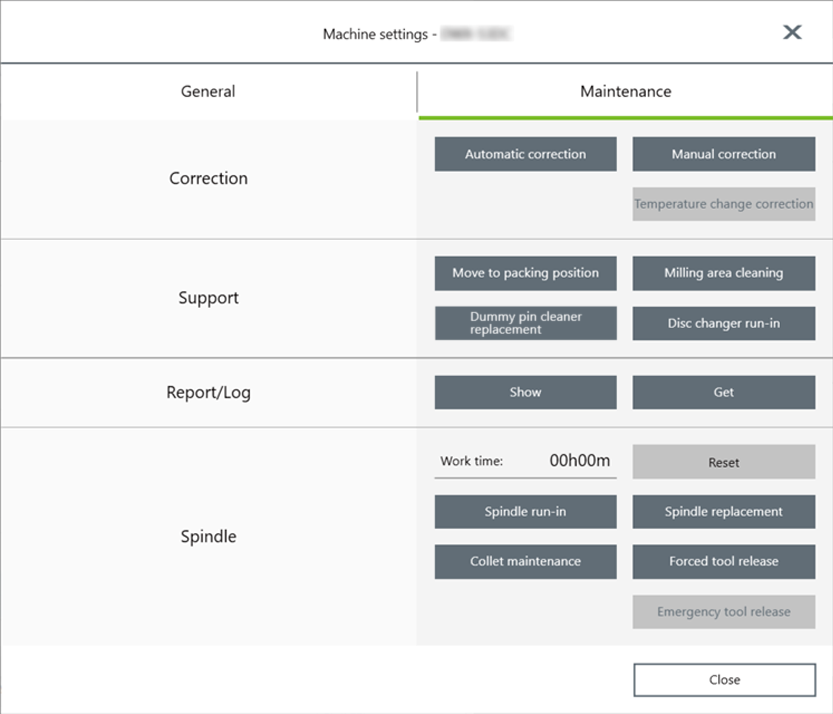
- Correction
-
- Automatic correction / Manual correction
- Correct the ATC magazine position or the rotary axis position. Normally use Automatic correction. Perform Manual correction to increase the milling accuracy.
- Support
-
- Move to packing position
- Moves the rotary axis unit, ATC magazine, and spindle unit to the packing position. Remove the workpiece and the correction jig before performing this work.
- Milling area cleaning
- Use this button when you clean the machine.
- Dummy pin cleaner replacement
- Replace the dummy pin cleaner. Replace the dummy pin cleaner if it becomes damaged and when the recommended replacement time is reached.
- Disc changer run-in
- Performs disc changer run-in (warm-up), which stabilizes the disc changer operation and maintains the milling quality.
- Report/Log
-
- Show
- Displays the error history as well as system information such as the firmware version and the total operating hours.
- Get
- Obtain a file in which the information of the various logs is collected.
- Spindle
-
- Reset
- Work time displays the work time of the spindle. After replacing the spindle unit, click Reset to reset the value to 0. For spindle unit replacement time guidelines, refer to the User's Manual of the model you are using.
- Spindle run-in
- Performs spindle run-in (warm-up), which stabilizes the rotation of the spindle.
- Spindle replacement
- Opens the Spindle replacement window.
- Collet maintenance
- Continuous milling will cause the collet to become loose, making it easy for the milling bur to come off. Use these buttons when retightening the collet and in other periodic maintenance. Follow the on-screen instructions to perform the maintenance work.
- Forced tool release
- Forces the spindle unit to release the tool it is gripping. Use this button when the spindle unit cannot release the tool it is gripping.
- Emergency tool release
- This button is enabled when the machine is turned on while a cover is open. Use this button if the initial operations cannot be performed because, for example, the milling bur is caught on the workpiece.